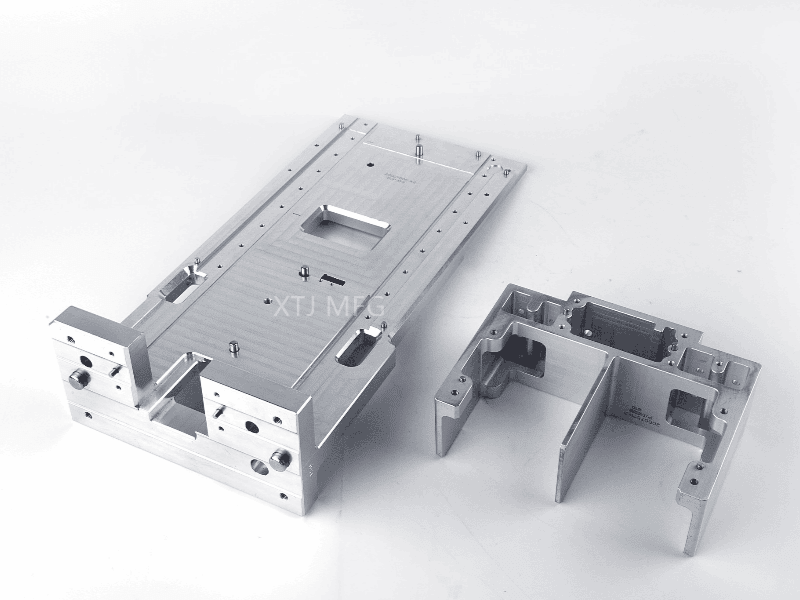
As 3D printing continues to revolutionize manufacturing, optimizing cost-efficiency becomes a top priority for businesses and enthusiasts alike. By employing smart design strategies, it is possible to reduce costs and make the most of this additive manufacturing technology.
In this article, we’ve outlined some of the top design tips and tricks to help you optimize your next 3D printing design to reduce costs and maximize efficiency.
Table of Contents
Reduction Design Tips for 3D Pringting
1. Reduce the Size of Your Print
If you are manufacturing a part for proof of concept, scale down your model. This can be easily achieved with 3D printing. Smaller prints will allow you to get through the prototyping phase faster and cheaper than a full-scale design.
2. Hollow Out Your Parts
By default, printing processes like Stereolithography will print completely solid components. Hollowing the model will significantly reduce the amount of resin required and print time, which reduces overall manufacturing costs.
optimizing 3d printing to reduce cost
3. Replace Solid Parts With Lattice Structures
Well-designed lattice structures can help reduce the weight of your part significantly whilst retaining structural integrity. It is also far less expensive to print than full solid objects. When considering incorporating lattice structures into your design, it’s important to consider the specific requirements and constraints of your application to ensure that they are suitable for the intended purpose.
4. Combine Multiple Parts Into a Single Print
One significant benefit of additive manufacturing is the ability to print fully assembled, multi-component parts in a single job. If your design consists of multiple components, try to combine them in a single print. This reduces the number of print jobs and eliminates the need for assembly, which can be a more cost effective.
5. Limit Tolerances
To minimize printing efforts and cost, avoid excessive tolerancing of parts. “Over-tolerancing” can lead to increased complexities and expenses in the printing process, especially in metal 3D printing where additional secondary machining operations may be required. Embracing the opportunities offered by additive manufacturing, such as part count reduction and less need for super accurate fits, can help optimize cost-effectiveness in the production of parts.
6. Use fewer walls
When it comes to processes. like FDM 3D printing, the walls typically consume the most material. By reducing the number of walls, you can achieve significant material savings and faster print times. However, it’s crucial to note that using fewer walls will also significantly reduce the strength of the part. Therefore, it is advisable to only decrease the number of walls if you’re sure the part will have enough strength for its intended application.
XTJ is a leading OEM Manufacturer that is dedicated to providing one-stop manufacturing solutions  from prototype to production. We are proud to be an ISO 9001 certified system quality management company and we are determined to create value in every customer relationship. We do that through collaboration, innovation, process improvements, and exceptional workmanship.