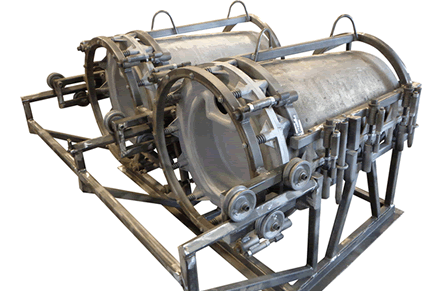
Table of Contents
What is Rotational Molding: Process, Materials Used, and Industrial Applications?
Rotational molding is a relatively simple process used to shape thermoplastics in a high-heat, low-pressure environment. It is considered to be a comparatively low-cost process to run. The low pressure on the mold means that aluminum can be used for the tooling. Rotational molding is used in several industries for products such as road cones, outdoor furniture, store mannequins, and kayaks.
This article will discuss rotational molding, how it works, its purpose, applications, and benefits.
What Is Rotational Molding?
Rotational molding is a process for molding thermoplastics in a low-pressure, high-heat environment (c. 482-550 °F). Tooling used for rotational molding is commonly made from aluminum alloys. and the vast majority of resin used in the process is polyethylene, which does not break down chemically at the temperatures used for molding.
Rotational molding is used for parts requiring standard, uniform wall thickness, a high degree of structural stability, and a high-quality finish. As the final piece is created in one continuous process, parts do not require joining by welding therefore there are no weld lines or pinch-off seams, (as might be present in blow molding) upon completion. Rotational molding is ideally suited for open double-walled containers, or larger, single-pieced hollow parts. Examples of rotational molding include coolers, tanks, and kayaks).
How Has Rotational Molding Developed Over Time?
Rotational molding has changed over time from when it was first used to manufacturing the durable plastic products we use today. Historians believe rotational molding dates back to the Egyptians, who used the process to create their ceramic pottery. However, the official patent was first documented in 1855 to create hollow vessels and metal artillery shells. In the 19010s, the concept of rotational molding was applied to the food industry, where hollow chocolate eggs and bunnies were produced using this method! In the 1940s, toys were among the first objects to be mass-produced by rotational molding, and by the 1950s, many household items were being made this way.
The types of materials used in rotational molding have developed over time, initially thought to have started with ceramics and then evolved to metals, waxes, and plaster. Today, aluminum is used predominantly, with the distinct features of rotational-molded products being their durability, flexibility, and ability to withstand high heat without cracking.
The process of rotational molding continues to evolve. There has been a sharp rise in the importance of environmentally friendly molding materials. Environmentally friendly and bioplastic alternatives that will become the successors of today’s plastic materials are currently in the process of being researched, developed, and introduced.
What Are the Key Materials Used in Rotational Molding?
Several different materials can be used in the rotational molding process. However, they must be capable of being pulverized into a very fine powder, ranging from 74-2000 microns. Some key materials are as follows:
Polyethylene: It is available in a variety of classifications and grades. Polyethylene is a type of thermoplastic from the polyolefin family.
Polypropylene: It has a high heat distortion temperature, high resistance to environmental stress cracking, and excellent resistance to chemical stress cracks. It is typically used for manufacturing food industry products.
Polyvinyl Chloride: This material can be processed in both powder and liquid forms. It is commonly used in applications such as pet toys, dolls, and other children’s toys.
Nylon: Two grades of nylon can be used in rotational molding: nylon 12 and nylon 6. They are known for their high rigidity, tensile, and impact strength. Nylon has a very high heat resistance when compared to other rotational molding materials such as polyethylene.
Polycarbonate: This material retains its mechanical properties at higher temperatures than most thermoplastics, and is consequently a more expensive material than polypropylene, polyethylene, and even nylon. Rotational molding is usually used to fabricate furniture, shipping containers, and light fixtures from polycarbonate.
What Products Are Produced By Rotational Molding?
Many types of products are produced by rotational molding. Some examples include the following:
Kayaks
Tanks (for example storage tanks in agricultural, commercial, or industrial scenarios)
Store mannequins
Coolers
Bins and containers
Road cones
Road barriers
Automotive parts (including interior design elements, such as cup holders)
Sports equipment (for example dumbbells, helmets, golf carts)
How Does Rotational Molding Work?
Rotational molding works by creating a low-pressure environment (around 1.51 P, which is around 50% more than atmospheric pressure) with very high heat (approximately 482-550 °F). Plastic material is put into a hollow mold, where it is then rotated on two axes and placed inside the hot, low-pressurized oven. The rotational molding mechanism ensures the mold is slowly rotated upon two axes whilst being simultaneously heated to distribute and then fuse the resin inside the mold. Once the plastic has been completely melted and evenly distributed across the mold, it is then removed from the oven and cooled either with water spray or in the air. Once completely cooled, the rotation stops and the mold can be opened to reveal the finished piece inside.
What Are the Steps in the Rotational Molding Process?
The rotational molding process is relatively straightforward to understand. The steps in the rotational molding process are listed below:
A hollow mold is filled with powdered plastic resin (usually made from cast aluminum).
Close the hollow mold, and a pressure of 1.51 P begins to gently rotate bi-axially. Transfer the mold into a high-heat oven, the temperature of which averages 500 °F.
The mold continues the slow rotation as the plastic resin melts and completely covers the walls of the mold.
Remove the mold from the oven and cool until the resin has hardened into the desired design.
Finally, stop the rotation and open the mold to reveal the finished product, which can then be removed and used or subjected to any desired secondary processes.
How Is Quality Control and Standardization Maintained in Rotational Molding?
Standards and quality must be maintained in rotational molding to ensure products are indeed durable, high quality, and reliable. Quality control refers to the checks in place to ensure product quality and standardization and can include reviewing the manufacturing processes, testing products, and establishing process tolerances.
One approach to ensure the production of high-quality rotational-molded parts is to ensure standards are maintained by ISO regulations. The relevant ISO standard for plastic molded parts is ISO 20457:2018(en) which relates to tolerancing standards. To maintain quality control and standardization in rotomolded products, manufacturers aim to comply with standards such as ISO, carry out regular reviews of processes (for example statistical process control), and ensure that manufactured parts meet the design tolerances. These approaches together will ensure any inconsistencies identified during the production phase can be rectified to ensure both customer satisfaction and manufacturer reputation.
Where To Look for Molding Services?
To find a rotational molding service that fits your needs, you can use the Thomasnet Discovery Platform here. Thomasnet®’s Discovery Platform can help put you in contact with one of over 70,000 North American suppliers. Using the Discovery Platform gives you access to filters that help you locate a supplier in the right location, with the right certifications, qualifications, and experience. The Thomasnet® Verification filters can help with verifying information provided by the companies on Thomasnet®’s platform.
What Are the Advantages of Rotational Molding?
In comparison to other molding methods, rotational molding has some advantages, including:
As a result of the low operating pressures at which rotational molding is conducted, the tools used in the process can be made from low-cost metals, for example, aluminum.
Rotational molding forms parts as one piece. This eliminates the requirement for joining subcomponents (for example by welding), which can create weak points.
Since the molded parts aren’t exposed to any external pressure, the parts produced have lower residual stresses. Therefore, the risk of defects in the finished product is reduced and can have multilayer or double-wall construction.
This method is suitable for both short or low-volume production, with little or no resin waste.
The process of rotational molding results in thicker corners on parts. This, in turn, decreases the risk of failure at stress-concentrated points.
Due to the constant mold rotation, it is easy for a manufacturer to control wall thickness whilst the plastic is in the oven.
Special surface finishes are easily produced in rotational molding, for example, logos, lettering, symbols, and intricately designed textures.
What Are the Limitations of Rotational Molding?
Despite its many advantages, rotational molding also has some disadvantages, including:
Rotational molding materials must have certain properties, which limits the choice of materials. These materials must be able to be readily converted into a fine powder from granules, and they must have a high degree of thermal stability.
The rotational molding speeds typically range from 4 to 20 RPM. The required speed for the specific product is often found through a trial and error process, which can be incredibly wasteful of both the manufacturer’s time and uses up oven capacity. Once selected, the final rotational speed is maintained constantly throughout the process largely due to a lack of understanding of how best to alter the speed during the cycle. An average of eight rotations per minute means that larger pieces can take up to 3 hours to complete.
Rotational molding tooling must be replaced or refurbished more frequently than harder materials, such as steel.
Automation is not yet applicable in rotational molding, therefore requiring more labor than other manufacturing processes.
Due to the requirement for rotational molding materials to be of high thermal stability, it is more costly for the required additives and grinding the material used into a powder beforehand.
What Industries Commonly Use Rotational Molding?
Because rotational molding is so incredibly versatile, it can be used to create a wide range of molded products across a multitude of industries, such as:
Utility: Rotational molding is used to create water and chemical supply tanks of up to 50,000 liters.
Boating: Buoys, pontoons, and floats are commonly produced by rotational molding.
Automotive: Diesel fuel tanks, tractor dashboards, and toolboxes are often fabricated by rotational molding.
Environmental Products: Road cones, traffic dividers, and litter bins are made using the rotational molding process.
What Is the Environmental Impact and Sustainability of Rotational Molding?
Rotational molding is widely considered to be an environmentally friendly and sustainable process for several reasons. First, no dangerous toxins or chemicals are released during the rotational molding process. Second, this process wastes less material as there is extremely minimal, or no resin scrap or waste. Thirdly, the rotational molding process eliminates the need for secondary tooling as the entire product is created in the same mold and does not need to undergo another process to weld various pieces together. Finally, rotational molding is considered sustainable as it is possible to employ recycled raw material for the process, and all products that have been manufactured in this way can be recycled.
What Are the Safety Concerns in the Rotational Molding Process?
As with all mechanical processes, rotational molding can be hazardous. First, there are safety concerns around those who have whole-body access to the oven compartment that heats the mold. Should someone get trapped inside the oven, the high temperatures would result in serious injuries, if not fatalities. Secondly, any moving or fixed powdered machine elements (for example carousel arms or automatic doors) could result in limbs being trapped. Other safety concerns in the rotational molding process center around the convective and radiant heat from the oven and the potential overpressurization of molds. These could both lead to injuries such as burns. Finally, gas and electricity connections present safety concerns in the event of human contact and therefore require protection from any heat or mechanical damage.
Why Do Manufacturers Choose Rotational Molding?
Rotational molding has several advantages that lead manufacturers to choose this process. Since rotational molding is carried out at low operating pressures, lower-cost metals can be used for molds, such as aluminum, which is much easier to source and cheaper to buy than materials such as iron, which tends to be more expensive. Additionally, once the rotational molding process is established, the quick setup allows for small batches to prevent overstocking of plastic products and to meet customer demands where smaller quantities are required. Another reason manufacturers choose rotational molding is that it is a low-waste process and is ideal for producing large, hollow parts with uniform wall thickness.
Does Rotational Molding Prove Its Efficiency in Manufacturing?
Yes, rotational molding is considered to be an efficient manufacturing process. One of the biggest advantages of rotational molding is that it allows for a swift lead time from design to production. While rotational molding requires the part to sit in the mold while being rotated for a comparatively longer time, once complete, the part is finished and ready to be used and does not require further attachment or joining to other parts. The efficiency of design to production time and the low material waste of the rotational manufacturing process allow manufacturers to stockpile less raw material and allow manufacturers to respond to and meet unpredictable product demand and produce both large and small batches of products. The ability to quickly change out molds from one product to another allows just-in-time manufacturing and delivering, reducing the need for warehouse space therefore saving any costs associated with that.
What Is the Difference Between Rotational Molding and Blow Molding?
Rotational molding and blow molding are similar processes that both produce hollow plastic parts. However, there are a few key differences between them. First, hollow plastic parts produced by rotational molding tend to be stronger, thicker, and more complex than those made by blow molding, which produces thinner-walled parts in relatively simple designs. Rotational molding tooling costs are lower than those for blow molding. Production cycle times also vary between the two, with rotational molding taking longer than blow molding. Additionally, rotational molding uses a much lower pressure (c. 1.51 P) than blow molding at 25 to 150 psi. Finally, while the materials both processes use are largely similar (nylon, polyethylene, and polypropylene, for example), the form factor differs. Rotational molding uses powdered resin, whereas blow molding uses pellets.
XTJ is a leading OEM Manufacturer that is dedicated to providing one-stop manufacturing solutions of Rotational Molding  from prototype to production. We are proud to be an ISO 9001 certified system quality management company and we are determined to create value in every customer relationship. We do that through collaboration, innovation, process improvements, and exceptional workmanship.