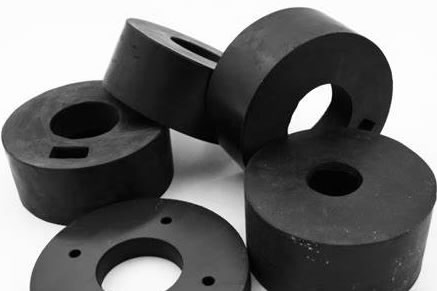
Rubber gaskets play a crucial role in sealing the interfaces between parts. Their primary purpose is to prevent leakage, ensuring airtight or watertight seals between two surfaces. These flexible components are commonly made from elastomers like: neoprene, EPDM (ethylene propylene diene monomer), silicone, or nitrile. Each material offers unique properties.
This article will discuss rubber gaskets, their purpose, types, properties, and applications.
Table of Contents
What Is a Rubber Gasket?
A rubber gasket is a mechanical sealing device designed to fill the gap between two mating surfaces. It creates a pressure-tight and resilient seal to prevent leakage of fluids or gases. Though “rubber gasket” is a common parlance, the term is often applied to other elastomeric polymers as well as genuine rubber. Materials are chosen for their flexibility, compressibility, and resistance to specific environmental conditions. Rubber gaskets are made in a wide variety of forms such as: sheet, ring, and custom molded.
Is a Rubber Gasket the Same as a Silicone Gasket?
No, not in all cases. Rubber gaskets are manufactured in a wide range of materials to suit various applications. Silicone rubbers offer particularly beneficial properties to suit some demanding industrial and consumer settings. So a silicone gasket IS a rubber gasket, but NOT ALL rubber gaskets are made from silicone rubbers.
What Is the Purpose of a Rubber Gasket?
Gaskets provide resilient and elastic compression seals between rigid parts. Under compression, they apply equal elastomeric pressure to both of the faces they contact. Rubber gaskets resist the application of differential pressure across the sealed junction, so they act as barriers to leakage. All manner of materials are blocked: gases, liquids, oils, aggressive and mild chemicals, powders, slurries, and all grades in between.
In addition, gaskets can serve as mechanical/wear joint protection elements by absorbing the relative motion of two parts while preventing their direct contact and abrasion. They provide a damping and self-centering force in applications where direct transmission of mechanical loading through a component junction is undesirable.
Why Are Rubber Gaskets Needed?
Parts are connected via rubber gaskets for several reasons:
They create a barrier that prevents the leakage of liquids, gases, or other substances, maintaining a secure and tight seal.
They prevent infiltration by contaminants such as: dust, dirt, liquids, or foreign particles. This is particularly crucial in sensitive environments, such as electronic enclosures or aerospace systems.
Rubber’s inherent flexibility allows gaskets to absorb vibrations and shocks, reducing the impact on mechanical components.
Depending on the material used, rubber gaskets can withstand a wide range of temperatures and resist chemicals, oils, and solvents.
Rubber’s compressibility allows gaskets to conform to irregular or uneven surfaces, ensuring a tight seal even against challenging geometries.
In certain applications, rubber gaskets can contribute to noise reduction by damping vibrations and preventing the transmission of sound.
How Are Rubber Gaskets Used in Manufacturing?
Rubber gaskets are typically used as seals in moderate-pressure and restricted-temperature sealing applications, where their simplicity and surface quality/alignment tolerance translate into reliability in imperfect conditions.
Any manufacturing plant that must seal fluids, gases, or powders from adverse flow at a coupling may use rubber gaskets. Rubber gaskets are used in joint and flange seals, conveyor belts, heat exchangers, and tank rims and covers.
What Are the Different Types of Rubber Gasket Materials?
Various rubber materials are used to manufacture gaskets. Some of the more common types are listed below:
Neoprene (Chloroprene): Excellent weather resistance, good oil resistance, and moderate temperature resilience. Suited to outdoor gaskets, automotive seals, and marine applications.
EPDM (Ethylene Propylene Diene Monomer): Superior weather resistance, excellent ozone resistance, and good chemical resilience. Suited to outdoor seals, HVAC systems, and automotive weatherstripping.
Nitrile (NBR): Good oil and fuel resistance, flexibility, and durability. Suited to oil seals, fuel system gaskets, and hydraulic seals.
Silicone: Wide temperature range (-60 °C to 230 °C), excellent flexibility and electrical insulation. Suited to high-temperature applications, electrical enclosures, and food-grade gaskets.
Viton® (Fluoroelastomer): Excellent chemical resistance, high-temperature stability, and resistance to oils and fuels. Suited to aerospace seals, chemical processing, and automotive fuel systems.
Natural Rubber: High elasticity, resilience, and tear resistance. Suited to general-purpose gaskets and vibration isolation mounts.
Butyl: Excellent gas and moisture impermeability and good chemical resistance. Suited to seals for vacuum systems and pharmaceutical applications.
SBR (Styrene-Butadiene Rubber): Good abrasion resistance, low cost, and moderate weather resistance. Suited to general-purpose gaskets and conveyor belts.
Polyurethane: High abrasion resistance, excellent load-bearing capacity and flexibility. Suited to seals for hydraulic systems and high-wear applications.
Hypalon® (Chlorosulfonated Polyethylene): Excellent weather and chemical resistance and good heat resistance. Suited to roofing materials and chemical processing.
EPDM/Neoprene Blend: Combines the weather resistance of EPDM with the oil resistance of neoprene. Suited to outdoor gaskets requiring oil resistance.
Nitrile/PVC Blend: Combines the oil resistance of nitrile with the flexibility of PVC. Suited to gaskets for oil-resistant and flexible seals.
What Makes Rubber Gaskets Unique Compared to Other Gasket Types?
There are key benefits to rubber gaskets that alternative materials cannot deliver. Rubbers can be formulated for high durability and excellent performance in both self-lubricating and liquid-lubricated applications. The diversity of material options allows rubber gaskets to perform well in particularly challenging environmental conditions, including: exposure to heat, cold, chemicals, and even radiation. Silicone rubber, for example, offers exceptional high-temperature resistance, making it great for demanding applications. It also remains flexible at very low temperatures.
Rubber’s inherent flexibility and damping properties make gaskets important in dynamic machinery. Rubber gaskets can be molded to fit almost unlimited geometries and requirements and a range of hardnesses from 20 Shore A to 90+ Shore A. Certain rubbers exhibit excellent electrical insulation properties, making them suitable for items that need to isolate electrical charges.
To learn more, see our full guide on Other Gasket Types.
What Are the Properties of Rubber Gaskets?
Rubber gaskets possess several key properties that make them suitable for sealing applications in various industries. Table 1 below outlines the properties of common rubber materials used in gaskets:
Neoprene Nitrile (NBR) EPDM Silicone Viton (FKM) Buna-N (Nitrile) Poly urethane Butyl
Elasticity âś…âś… âś…âś… âś…âś… âś…âś… âś…âś… âś…âś… âś…âś… âś…âś…
Flexibility âś…âś… âś…âś… âś…âś… âś…âś… âś…âś… âś…âś… âś…âś… âś…âś…
Durability âś…âś… âś…âś… âś…âś… âś… âś…âś…âś… âś…âś… âś…âś…âś… âś…âś…âś…
Insulate ✅✅ ✅ ✅✅ ✅✅✅ ✅✅ ✅ ❌ ❌
Thermal Resist âś… âś… âś…âś… âś…âś…âś… âś…âś…âś… âś… âś…âś… âś…âś…
Chem Resist âś…âś… âś…âś… âś…âś… âś… âś…âś…âś… âś…âś… âś… âś…âś…âś…
Weather Resist âś…âś… âś…âś… âś…âś…âś… âś…âś…âś… âś…âś…âś… âś…âś… âś…âś… âś…âś…
Comp Set ✅ ✅ ✅ ❌ ❌ ✅ ❌ ❌
Tensile Strength âś…âś… âś…âś… âś… âś… âś…âś… âś…âś… âś…âś…âś… âś…âś…
Cold Flex âś… âś… âś…âś… âś…âś…âś… âś…âś… âś… âś…âś… âś…âś…
Table 1: Properties of Common Rubber Materials
Key: âś…âś…âś… = excellent
âś…âś… = good
âś… = moderate
❌ = poor
What Are Rubber Gaskets Made Of?
Rubber gaskets are manufactured from a wide variety of thermoset, vulcanized, and thermoplastic elastomers. Each type of rubber has unique properties and characteristics. The two broadest categories are:
Synthetic Rubber: Produced through the polymerization of synthetic monomers these materials can be tailored to specific applications. Some examples are: nitrile rubber (NBR), butadiene rubber (BR), styrene-butadiene rubber (SBR), ethylene propylene diene monomer (EPDM), polyurethane rubber (PU), silicone rubber, and styrene-butadiene rubber (SBR).
Natural Rubber (NR): Derived from the latex of rubber trees (Hevea brasiliensis), natural rubber is known for its high elasticity, compression set resilience, and tear strength.
Is a Rubber Gasket Waterproof?
Yes, rubber gaskets are widely employed in aqueous industrial processes and water supply systems specifically because they’re waterproof. They are universally capable of sealing water pressure when correct geometry and suitable compression are applied.
What Is the Standard Thickness of a Rubber Gasket?
There is no standard thickness of gaskets in general, including those manufactured from rubber. Several factors influence the thickness. A gasket requires some compression force to be able to resist differential pressure across its sealed orifice, junction, or transition. If this compressive force exceeds the material’s capacity, it will cause internal shearing and mechanical failure. This effect can be countered by making the gasket thicker so it can distribute more compressive load and reduce localized strain levels.
How Do Rubber Gaskets React to Different Temperatures?
Many thermoplastic gasket materials are severely temperature-limited and will break down and soften at even moderately elevated temperatures. Most synthetic thermoset rubbers, however, are capable of withstanding higher temperatures, as their cross-linked structures don’t undergo the same softening as thermoplastics. Some synthetic elastomers, such as silicone rubber and thermoset fluoroelastomers, continue to function at temperatures exceeding 300 °C.
Similarly, rubbers have varied performance at low temperatures. Thermoplastic rubbers generally stiffen at low temperatures, so cold performance must be selected carefully. Thermoplastics are rarely suited to freezing conditions. Thermoset rubbers vary considerably in low-temperature performance, with silicone and fluoroelastomers offering the best range of operational temperatures.
What Are the Industrial Applications of Rubber Gaskets?
A comprehensive list of industrial applications for rubber gaskets could fill a book, so a few examples are offered as a guide:
Oil Fields: Gaskets join flange connections to create tight seals between pipeline sections, valves, and other equipment. These gaskets prevent leaks of hydrocarbons and other fluids. Rubber gaskets used in pipeline applications are designed to withstand high pressures, temperature fluctuations, and environmental conditions such as snow and sunlight.
Hydraulic Systems: Rubber gaskets are employed to seal the interfaces between the hydraulic cylinder barrel and piston, as well as between the piston and cylinder end caps. These gaskets conserve hydraulic fluid pressure to keep the system’s motions precise.
Hydraulic hose assemblies are used to carry hydraulic fluid pressure between components, such as: pumps, cylinders, and valves. Rubber gaskets create seals between hose assemblies and hydraulic system components. These gaskets prevent fluid leakage at hose connections, ensuring reliable fluid transfer and maintaining hydraulic system pressure and performance.
Jet Engines: Rubber seals are used in multiple locations throughout jet engines, including: in combustion chambers, turbine sections, bearing compartments, and accessory drives. They serve various functions, such as: preventing air, fuel, and exhaust gas leaks, retaining lubricants, excluding contaminants, and maintaining proper clearances between rotating components.
In combustion chambers, rubber gaskets create seals between fuel nozzles, liners, and casings, containing the combustion process and preventing hot gas leaks. These are among the highest-temperature applications for rubber gaskets.
How To Install a Rubber Gasket
Rubber gaskets exist in multiple forms and the installation procedures depend heavily upon the geometry of the gasket itself, its placement in the equipment, and the materials involved. Some common examples are discussed below:
Flat Face Gasket: This low-precision type of gasket operates under relatively low stress. Axially compressed rubber-ring seals in pipe connections are found everywhere. In these cases, the seal is generally placed inside a threaded female receptacle wherein it is size-constrained (i.e. bulge-limited at least at the outer rim). The female thread is then screwed onto the male counterpart to make the joint and the gasket is compressed at the contact faces. This type of gasket finds application across piping systems of all scales, from laundry machine water connections to oil and gas pipelines, but their basics remain the same.
O-ring in a Shaft Groove: An O-ring is seated in a machined groove to provide an annular seal. To seat it, the ring must be stretched over the shaft (and any additional features on that shaft) and then slid along until it seats into the groove. It is common to apply some lubrication to enable this installation (as long as the lubricant doesn’t jeopardize the seal). Once installed into the shaft groove, the O-ring will generally sit in a cylindrical recess as the shaft is installed, undergoing appropriate compression to create a seal. The lubricant applied during the first installation serves to prevent longitudinal sliding damage to the outer face of the seal as it is seated.
V-form Oils Seal: Oil seals for rotating shafts commonly take on an open V-form shape. The outer-diameter ring is rigid and the open side of the V-form faces the higher pressure side. This allows the applied journal pressure to open the V and increase seal pressure. Such seals are generally press-fitted into a female opening and then lubricated to receive the shaft as it passes through the open seal. Great care is required to avoid nicks in the edge that contact the shaft and to avoid pre-damaging the seal and degrading its operational life.
When To Use a Rubber Gasket
Rubber gaskets are used when adaptable seals are needed. For example, they are extensively used in plumbing systems to create watertight seals between pipes, fittings, valves, and fixtures. Such gaskets are applied extensively in industrial machinery and equipment to seal joints, prevent fluid or gas leaks, and provide cushioning and insulation against vibrations.
Does a Rubber Gasket Require a Sealant?
It depends on the exact nature of the application and the type of rubber gasket. In most cases, rubber gaskets are designed to provide effective seals without the need for additional sealants. However, there are situations where sealants may be used. For example, if you need extra assurance of the seal’s performance, an additional sealing agent may help. If the mating surfaces are uneven or have imperfections that could compromise the seal, applying a sealant along with the rubber gasket can help fill in gaps.
What Is the Lifespan of Rubber Gaskets?
It depends. Gaskets’ operational lifetimes are affected by factors such as: aggressive media, temperature, and motion-induced wear. Simple face seals that are compressed in water-supply pipe joints can survive for decades.
Cars and other machines often need shaft oil seals that run a hard rubber seal face on a polished, hardened steel shaft. Such is the case for engine crankshaft seals, which demand pressure-fed, oil-lubricated bearings. These seals commonly endure for the entire lifetime of the vehicle and are still serviceable after the engine is considered scrap.
What Are the Signs of Rubber Gasket Failure?
Rubber gasket failure can manifest in a variety of ways, depending on the application and the environmental conditions. One of the most obvious signs of rubber gasket failure is leakage. This can come in the form of fluid, gas, or air leaking from the sealed area or it may only be evident from pressure loss. The first signs of this are likely to be visible leakage. In high-pressure applications, the gasket may bulge or extrude from the sealing area, indicating that it’s unable to withstand the pressure and maintain an effective seal. Equally possible is the chemical degradation of the gasket material, resulting in bulging due to swelling.Over time, rubber gaskets may flatten or creep under pressure, causing the seal to deteriorate and potentially leak.
Rubber gaskets commonly fail when exposed to extreme temperatures outside of their operating range. This can result in: hardening, softening, cracking, or other forms of deterioration. Excessive vibration or movement that wasn’t accounted for in the specification can cause the gasket to wear prematurely or become dislodged from its sealing position.
Do Rubber Gaskets Need To Be Replaced?
Yes, rubber gaskets are commonly replaced as part of repairs or preventative maintenance. In many devices, gaskets are simply considered service items. In an automotive gearbox, for example, various gaskets will be systematically replaced during regular servicing. In other, less demanding applications, the replacement of gaskets may be an unnecessary precaution as their service durability is very high.
What Are the Benefits of Rubber Gaskets?
Rubber gaskets serve several functions. Their value depends on the system’s specifics, but the most common benefits are:
Flexibility
Compressibility
Elasticity
Chemical resilience
Temperature resilience
Weathering resistance
Abrasion resistance
Tear resistance
Electrical insulation
Vibration damping
Sealing performance
Material compatibilities
What Are the Downsides of Rubber Gaskets?
While rubber gaskets are an unavoidable necessity in many applications, their limitations must be considered:
XTJ is a leading OEM Manufacturer that is dedicated to providing one-stop manufacturing solutions of  Rubber Gaskets Parts from prototype to production. We are proud to be an ISO 9001 certified system quality management company and we are determined to create value in every customer relationship. We do that through collaboration, innovation, process improvements, and exceptional workmanship.