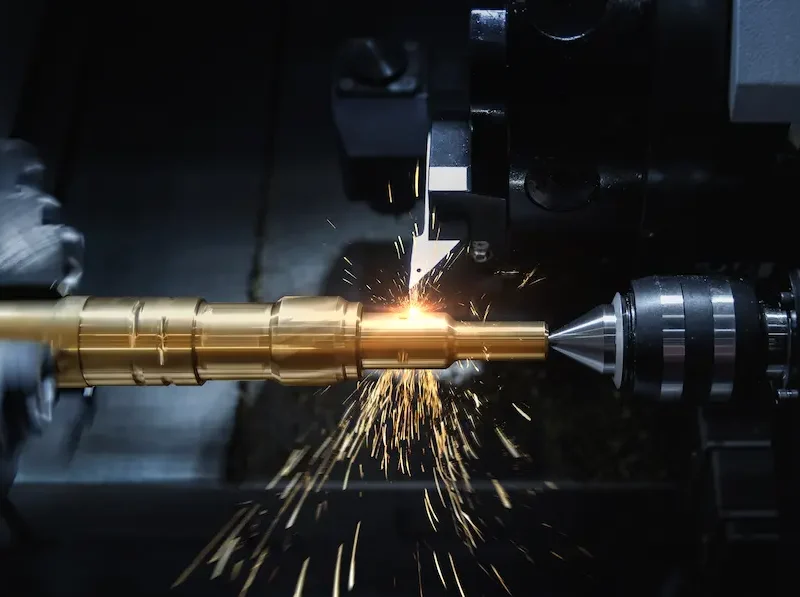
During the last few decades, the advent of CNC machining techniques in manufacturing has allowed for many existing industrial processes and techniques to be developed and used in a new form in modern-day manufacturing. While the main advent is the automation of many processes and rendering them more precise and quick, turning operations, in particular, have seen an improved quality over time.
Nowadays, CNC turning lathes can operate automatically, and efficiently with an increased yield. The induction of CNC techniques and tool paths into lathe turning has facilitated many aspects of this process and enabled it to produce even more complex parts. This has become the industry standard during the last few decades. Although the same turning principle applies in CNC, the technological advent of this new model has extended the reach of turning through CNC, and also made new uses possible for it.
Table of Contents
What is Lathe Turning ?
The earliest processes relied mainly on the rotation of a workpiece, of wood, metal, plastic, or stone, on a lathe. A cutting tool is then traversed along several axes. As it makes contact with the workpiece, the cutting head makes precise cuts along the workpiece to create the desired shape. Traditional methods relied mainly on manual lathes to rotate the workpiece. This usually required an operator to keep the workpiece in rotation and make the cuts along the workpiece. With CNC lathes, the process is automated. The high-speed rotation and the precision of the machine allow this method to work through solid materials like metals.
The single-point cutting head can operate at several angles, like a rake angle, or relief angle, with each producing a different effect on the workpiece. The cutting edge angle and size are chosen based on several factors, notably the desired shape. The main parameters in turning operations are speed and feed. These refer to the speed of the workpiece’s rotation, and the distance a cutting tool can advance into the workpiece in each revolution (cutting depth). These are determined by the material of the workpiece, spindle, and other variables relating to the specific setup.
Turning is one of many machining processes that rely on high-speed rotation and a cutting head to create the final shape of a piece. The currently applied turning processes can make use of more than the standard single cutting point configuration. Tapered turning for example can create a cylindrical shape, decreasing in diameter from one end to the other, and facing involves moving at a perpendicular angle to the workpiece’s rotary axis, to hollow out parts of an external surface. This same principle can be adjusted and modified to achieve several geometries and effects. This is the case for most manufacturing operations, where the lathe can be used for other similar processes like knurling and boring.
Different Turning Operations
Turning generally involves a rotating workpiece, and cutting along the plane. This process can be used to create different types of geometries and make the piece’s final shape. This method involves several processes that rely on the same principle. The basic turning process can also be classified into sub-processes. In addition to tapered turning, which involves making cuts of different diameters on the same workpiece, CNC lathes have also enabled the process of spherical generation. The latter can create pieces with geometrically true spherical shapes. Polygonal turning is now one of the latest innovations in manufacturing. It can produce non-spherical geometries, without interrupting the workpiece’s rotation. This method requires very accurate measurements to make the cuts at the same radial position during each rotation.
Hard turning is another widely applied variety of this process. It is mostly used with very hard materials. Before hard turning, most pieces go through a heat-treatment process. Although this method is often compared with grinding, they differ in some key aspects and are rarely used for the same purposes. Hard turning is optimal for pieces requiring a roundness accuracy of 0.5 – 12 micrometers, and a roughness range of Rz 0.8 – 7.0.
The turning operation can also involve a variety of slightly different operations which all rely on the same principle. These can include parting. This process involves making deep cuts in a specific section of the bar stock to cut it off completely. Grooving, a slightly different process, consists of making similar deep cuts, or grooves, in the bar stock, but without cutting it off completely. This general principle can be used to crave several types of carvings or patterns into a workpiece (as in the knurling process). These are mainly turning-specific processes. Besides the common similarity of being conducted on a lathe, they are applied mainly to create the final shape of a product and can differ from other similar lathe-based processes.
Difference Between Turning and Other Processes
Although the turning process is similar and often complementary to several other machining processes that are conducted on a lathe, some operations are not classified as part of the turning-specific processes. These different classes of turning operations are often connected in a manufacturing workflow. Their differences come from the capabilities of each process and their optimal uses.
Whereas turning is mostly reserved for making cuts along the external surface of a workpiece, there are similar lathe-based processes, with the same principle, that are applied to internal surfaces. This process is known as boring, and it constitutes, along with turning, the basis of several machining processes known as lathing. Boring is conducted using a single-point cutting tool, or a boring head, and can produce complex geometries as well. It is often used in line with drilling; the removal of material from the inside of a workpiece, or reaming; creating internal cavities of specific diameters, for an existing hole. Each of these processes used a different type of cutting head configuration. The focus on the internal surface of a workpiece demands a slightly different configuration of the machining process, although the basic principle is still the same.
Common Applications
Turning, and its derivative processes, are some of the most widely applied machining processes. They have been used before the advent of CNC. The latter has mainly advanced the potential of these techniques and made them even more widely adopted in manufacturing and industry. As such, these processes are needed to produce most industrial parts, components for equipment and vehicles, as well as many everyday appliances.
Several industries rely on parts and components of specific roundness accuracy, often made from very solid material. This is the main advantage of CNC turning, specifically hard turning, which makes it optimal for producing components for injection pumps or hydraulics. The aerospace industry, in particular, requires many parts and components that often go through a turning process. These can include aerospace shafts, fasteners, hollow shafts, and joint connectors.
The same applies to the automotive sector, which has a high demand for elements like hydraulic valves, throttle control shafts, low pass filter shafts, and other mechanical gears that are produced by turning. This technique is also used to produce parts for other equipment for the medical sector, military and technological sectors. The fact that turning is a very customizable process and fairly simple makes it one of the most common ones. Nowadays, almost every industry requires some parts and components that are produced by CNC turning.
Advantages and Limitations
The advent of CNC techniques in turning operations has made it one of the most flexible processes. Its main advantage is the fact that this technique can apply to almost all materials used in industry and manufacture. Turning can also produce parts and components with tight tolerances in a very short time. It is a very easy operation to perform (in most configurations) and does not require very high skilled workers, nor continuous supervision. The material removal rate is also flexible and can be customized to very accurate measurements.
Despite the convenience of this method, it can be difficult, as sometimes parts may require several operations and machines. Different cutting edge settings could be required, which is often costly. In most configurations, the turning process can only produce radially symmetrical parts, with the size range being limited. Although the turning process is limited by the shapes and sizes it can produce, it is nonetheless a very versatile method that can produce many modern-day appliances.
General Guidelines
Although turning is one of the simplest machining operations and made even easier with the advent of CNC, there is some level of attention to detail and precise measurements required. The angle of the cutting head, as well as the cutting speed and feed of the machine, can all affect the final result. As the turning can often be classified into two types; roughing and finish. Each type requires specific measurements
For example, ordinary steel and metals require a cutting speed of around 30 to 60 m/min, while cemented carbide turning tools can reach a speed of up to 80 to 200 m/min. This is largely determined by the workpiece material, the desired finished product, and the machining setup.
Conclusion
Turning is still one of the most widely applied industrial and machining processes today. It continues to be very relied upon, and able to cater to the increasing demand and requirements of most industries. Despite its limitations, turning capabilities and lathing equipment is still a necessity for most manufacturers. The advent of CNC has only made this technique even more powerful, and a lot more reliable.