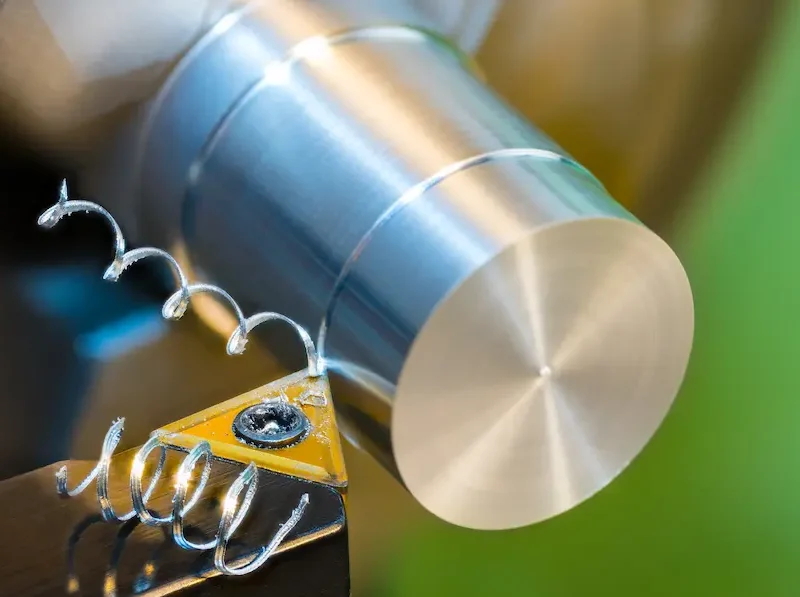
Lathes have been used to turn metal pieces for several centuries. Metalworking in general has always since relied on lathes, and turning operations, to produce pieces and components made of Metal. As one of the most solid materials we have, metals require a lot of force and speed to accurately fashion into industrial pieces and parts. With the induction of modern industrial methods, lathes have developed. This progress doesn’t only include the additional capabilities of lathes, but also other operations that lathes are now equipped to perform.
Metals are the materials that truly test the capabilities of industry and manufacture. Industries that often rely on solid durable metal pieces with specific measurements, high-quality standards, and tight tolerances consistently push for the improvement of metal production processes, many of which rely on lathes.
Metal or steel turning is an essential industrial process, and most manufacturers around the world are equipped to perform certain metal turning and lathing capabilities. With the advent of CNC techniques, metal turning is now far superior, more accurate, and reliable. This has essentially enabled metal turning operations to produce even more complex geometries efficiently.
Table of Contents
What is metal turning
Metal turning processes are diverse, each with specific usages and applications. The key aspect they share is that they all rely on the same turning and lathing principles, but are more specialized to use on metals. The basic principle involves high-speed rotation of the metal workpiece, and a cutting tool, or boring head, to make cuts along the several axes. This process often relies on a lathe designed specifically for metalworking.
Metal and steel turning generally refers to an ensemble of lathing processes like boring, reaming, knurling, and grooving all of which rely on the same principle and are often performed as part of the same process. Modern metalworking lathes, notably with CNC capabilities, can automate various metalworking lathe projects in the same machine. One of the main strengths of metal turning operations is to produce circular geometries. This is still true, although metal turning techniques can now produce several complex geometries. The process is currently adapted to apply to a wide variety of metals including ferrous metals like cast iron and steel, copper and nickel alloys, aluminum, and others. It is relied upon to produce parts and components for many industries and constitutes one of the essentials of metalworking.
Process description
There are several types of metal lathes, each with a different configuration and specific uses. Nonetheless, the turning principle is still maintained in all of these machines and their operations. The most common type of metalworking lathes is what is known as a center lathe or an engine lathe. This is essentially an automated lathe with a cutting tool. The metal lathe consists of a fixture, to which the workpiece is attached. Metalworking lathes function by rotating the metal workpiece, and the cutting tool then slowly subtract material from the workpiece’s outer surface. This usually causes small bits of metal, chips, or swarf, to cluster around the cutting tool. The purpose of this operation is to reduce the size of the workpiece to the required dimensions.
This process is generally limited in the amount of material it can remove. It tends to be operated as a secondary process. Industrial pieces often go through several processes to form their basic shape. Turning is commonly the last process for metal pieces and is used mainly to refine the surface or add other details.
Materials and specifications
Turning is a very common machining and industrial process and is often applied to several materials including plastic and some types of stone. Metal turning on the other hand is specific to metalworking. This impacts not only the process details, but metals also come in a wide variety. Turning operations can be applied to most metals. Yet, the characteristics of each type of metal can affect the process and require some special attention.
Unalloyed steel, for example, is commonly used in industrial operations and is noted for its high carbon content. Metals with high carbon require more force and machine feed to break. Unalloyed steel often requires the highest feed possible, and a wiper insert, to avoid chips clustering on the edge. Low-alloyed steels are quite different in this regard. The alloy contents and heat treatment determine the machinability of these metals. Grade steel series are the most used non-hardened low-alloyed metals.
High-alloyed steels are more solid, and generally include an alloy content of over 5%. The harder they are, the more difficult they become to machine and turn. Solid grade steel inserts are also for high-alloyed steel when the machinability becomes very difficult. Stainless steels are also common in metal turning operations, including austenitic stainless steels with a nickel alloy content of over 20%. These usually rely on the use of a round insert. Most solid metals rely on a specific type of insert (usually made of cast iron or CBN). Tool decay is usually anticipated when working with very solid materials. As such, there are specific steel grades used for different types of usages, be it intermittent cuts, complex geometries, or rake angle cutting.
Different turning operations
Turning is an essential industrial and machining process and includes several similar processes. Although metal turning refers to this process when it is exclusively applied to metals, the advances in manufacture and technology have made the capabilities of turning more or less applicable to a wide variety of materials. Also, the advent of CNC has centralized several turning-specific and non-specific operations into the wider group of metalworking lathe projects.
There are some subtle differences between the basic metal turning process and related operations, but they all rely on the same basic turning principle. For example, step turning creates several surfaces in a circular piece, each with a different diameter; the final product ends up resembling steps, while contour turning relies on the use of tracers to create the desired shape on a rotating workpiece. Some turning operations like grooving and parting can be used along with other processes, which makes them more of a commonly used technique, while other operations like boring and reaming are more specifically used for internal surfaces.
Advantages and Limitations
As one of the most commonly adopted industrial processes, metal turning operations are some of the most advantageous and economically efficient industrial processes. They are more efficient and produce less waste compared to other methods like forging, stamping, or casting. Most of the waste is generated during the cutting process, in the form of metal chips. These however can be collected and recycled. Another advantage of metal turning is cost-efficiency. It is one of the most tool-reliant industrial processes. Yet, tool costs are often low. Such tools are characterized by extreme hardness and durability (as they are designed specifically to work with solid metals). This tooling simplicity makes metal turning makes it less costly than other industrial processes.
Despite the flexibility and durability of tools involved in metal turning, this operation also has limitations. Perhaps the most prominent is the surface snarl or indent. A CNC metal lathe can require highly skilled workers to operate, especially when producing complex geometries. High rotation, miscalculated feed rates, and a very solid metal can often leave imperfections on the surface or shape of the workpiece. It’s often difficult to keep consistent spinning conditions. Tools can sometimes overheat. Shock between the cutting tool and very solid metal in high-speed rotation can also impact the machine’s speed, among other factors.
Common Applications
Metal turning operations are applied to produce most metal industrial pieces, notably ones with circular geometries. Many everyday appliances use turned metal pieces. For example, lighting fixtures and functional gear trays are both created by spinning metal pieces. This also applies to lighting bollards, which need turned metal pieces for caps and glare controls.
HVAC systems are almost entirely made of metal and consist of large circular metal tubes and outlets that are exclusively created by turning metal pieces. This process is also relied upon for industrial needs. Fan covers for induction motors and process hoppers are also made from turned metal. This process can also be used to create metal pieces for architectural uses.
Conclusion
Turning is an essential industrial process, provided and mastered by most manufacturers. The consistent technological advances continue to make turning, and other industrial operations like it, more accessible, and further developed, enabling them to perform more complex tasks. In most industrial processes, metals are some of the most reliable materials, but they are also challenging to machine and work with. Metal turning operations developed as an offset of the general lathing operations, designed specifically for the use of different metals. This development; the ability to machine and manipulate metals to form parts and components, has been as revolutionary in manufacture as in several other industries