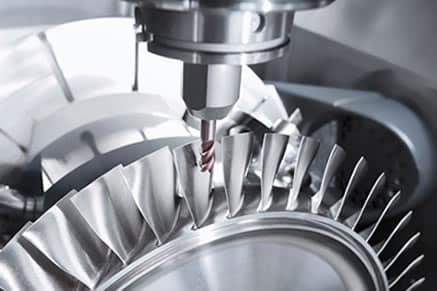
How to Operate 5-Axis Milling?
5-axis milling is one technology that has changed the game by offering incredible capabilities. 5-axis milling stands out as one of the most demanding endeavors within milling operations. This sophisticated machining demands not just profound skill but also precise application.
The outcomes attainable through the 5-axis Milling are truly remarkable. It introduces entirely fresh avenues for creating complex components, ones that would prove exceedingly challenging or unattainable through alternative manufacturing techniques. Five-axis milling delivers outcomes of utmost precision engineering and excellence, all achieved with optimal efficiency, making it a cost-effective choice.
This method goes beyond old limitations, letting engineers and designers bring their boldest ideas to life. In this discussion, you will learn all about 5-axis Milling and how it makes it possible to create intricate parts that were once thought impossible with traditional methods.
a 5 axis milling machine in operation crafting intricate components
Understanding 5-Axis Milling
5-axis milling is a sophisticated CNC machining method used in crafting complex parts. Unlike conventional 3-axis Milling, which operates solely along three linear axes (X, Y, and Z), 5-axis Milling integrates two additional rotary axes, thereby enhancing flexibility in tool movement. This expanded range of motion empowers the cutting tool to approach the workpiece from varied angles, facilitating the fabrication of intricate shapes and contours that would pose challenges or prove unachievable with fewer axes.
5-Axis Milling pertains to workpiece setup and fixturing. Securing the workpiece adequately is paramount to ensuring stability throughout the machining process and mitigating vibrations or deflections that could compromise accuracy. Specialized fixtures and clamping systems are frequently employed to firmly hold the part in place while facilitating access to multiple facets for machining.
Advantages of 5-Axis Milling
5-axis Milling is an advanced manufacturing technique that not only enhances accuracy and precision but also delivers superior surface finishes and reduces setup time. Here are the distinct advantages that 5-Axis Milling presents across industries.
Increased Accuracy and Precision
In comparison to traditional machining techniques, 5-axis milling excels in offering heightened levels of accuracy and precision. With the capability to maneuver the cutting tool in multiple directions simultaneously, it ensures meticulous machining of every aspect of the part according to exact specifications. This level of precision is particularly indispensable in the medicine and aerospace industry, where even the slightest deviations can yield significant consequences.
Photo showing a highly intricate part manufactured using 5 axis milling highlighting precision engineering
Photo showing a highly intricate part manufactured using 5 axis milling highlighting precision engineering
Enhanced Surface Finish
An additional advantage of 5-axis Milling lies in its capacity to achieve superior surface finishes. By dynamically adjusting the toolpath and angle of approach, it effectively reduces tool marks and inconsistencies, resulting in impeccably smooth surfaces. This feature holds paramount importance in applications where aesthetics or interaction with other components is crucial, such as automotive or consumer electronics.
Reduced Setup Time
Compared to conventional machining methods, 5-axis milling significantly reduces setup time. With the ability to access multiple faces of the part without necessitating repositioning or resetting, setup times are notably shortened. This not only enhances efficiency but also diminishes the likelihood of errors associated with manual adjustments, ultimately leading to expedited production cycles and reduced costs.
Ability to Machine Complex Geometries
Arguably, the most notable advantage of 5-axis Milling is its capability to machine highly intricate geometries effortlessly. Traditional machining techniques often encounter challenges with intricate designs or features that demand multiple setups and tool changes. However, 5-axis Milling addresses this issue by enabling the machining of complex shapes, curves, and contours in a single operation, thereby eliminating the necessity for additional processing steps and mitigating the risk of errors.
Application of 5-Axis Milling
5-Axis Milling is known for its versatility and efficient solution for the production of complex parts and molds across diverse industries. Its ability to deliver unparalleled precision, versatility, and efficiency makes it an indispensable tool in advanced manufacturing. Here are its detailed applications to several industries.
Aerospace
In the aerospace industry, 5-axis Milling stands as an indispensable tool. This technology facilitates the fabrication of complex aerospace components, such as turbine blades, engine parts, and structural elements. The capability to manufacture these components in a single setup ensures precise tolerances and superior surface finishes, bolstering the overall performance and safety of aerospace systems.
a finished aerospace component produced with 5 axis milling exemplifying advanced manufacturing
a finished aerospace component produced with 5 axis milling exemplifying advanced manufacturing
Medical Device Manufacturing
Medical device manufacturing extensively relies on 5-axis Milling to create a diverse range of products, from prosthetics to surgical instruments. This technique enables the production of customized implants and intricate surgical tools with unparalleled accuracy. Moreover, 5-Axis Milling caters to the intricate demands of the medical industry by manufacturing complex orthopedic implants and dental prosthetics.
Automotive
In the automotive sector, 5-axis Milling plays a crucial role in fabricating essential components like engine blocks and transmission parts. This technology empowers automotive manufacturers to realize complex designs and lightweight structures, thereby boosting vehicle performance and fuel efficiency. Additionally, 5-axis Milling facilitates the creation of complex molds for automotive body panels and interior components, enhancing both aesthetics and functionality.
Mold and Die Production
5-Axis Milling assumes a crucial role in mold and die production across various sectors, including automotive, aerospace, and consumer goods. It facilitates the fabrication of highly complex molds with precise contours and intricate details, ensuring the production of top-notch parts with minimal post-processing requirements. Furthermore, 5-axis Milling expedites the rapid prototyping process for molds and dies, accelerating product development and reducing time-to-market for new products.
Challenges and Considerations of 5-Axis Milling
While this advanced multi-axis Milling offers remarkable advantages in crafting complex parts, it also presents a unique set of challenges and considerations. Here are the challenges and considerations to address to achieve superior outcomes in terms of precision, efficiency, and part quality.
Machine Capabilities and Limitations
5-axis milling provides major benefits, but it also comes with challenges that involve the machine’s performance and limitations. It’s important to consider how strong and stable the machine is, especially when working with large or heavy items. The machine must be sturdy enough to handle the force of high-speed cutting while staying accurate over time. Manufacturers should carefully check if their machines are up to the task for the jobs they plan to do.
a high precision component machined using 5 axis milling technology
a high precision component machined using 5 axis milling technology
Toolpath Generation
Developing optimal toolpaths for 5-axis Milling can be a complex and time-intensive endeavor. Unlike conventional 3-axis Milling, where toolpaths are relatively straightforward, 5-axis machining introduces additional degrees of freedom, necessitating careful consideration of tool orientation and axis movements. Advanced CAM software equipped with integrated simulation capabilities can streamline the toolpath generation process and preemptively identify potential issues before machining commences.
Workholding Strategies
Effective work-holding is important for maintaining the stability and accuracy of parts during 5-axis Milling operations. However, the heightened complexity of part geometries and machining orientations can pose challenges for conventional workholding methods. Specialized fixtures and clamping systems may be indispensable for securely holding parts in position while ensuring accessibility to all machining surfaces. Manufacturers must meticulously assess work-holding strategies to enhance efficiency and uphold consistent part quality.
Comparison of 5-Axis Milling with 3-Axis and 4-Axis Milling
When it comes to CNC milling operations, the number of axes used plays a crucial role in determining the complexity and capabilities of the machining process. Here is a comparison of 5-axis Milling with 3-axis and 4-axis Milling, highlighting their differences and advantages:
Number of Axes
3-Axis Milling: In 3-axis Milling, the cutting tool moves along three linear axes – X, Y, and Z. This restricts the tool’s movement to three directions, making it suitable for machining simple geometric shapes.
4-Axis Milling: 4-Axis Milling introduces an extra rotary axis, usually the A-axis or B-axis, allowing the cutting tool to tilt or rotate. This enables the machining of more complex geometries by accessing different sides of the workpiece.
5-Axis Milling: 5-Axis Milling adds another rotary axis, typically the C-axis, to the capabilities of 4-Axis Milling. This additional axis enables the cutting tool to tilt and rotate in multiple directions, providing even greater flexibility for machining complex parts with intricate contours and undercuts.
Machining Capabilities
3-Axis Milling: Best suited for machining simple parts with flat or prismatic geometries and limited to cutting operations from one direction at a time.
4-Axis Milling: Allows for more complex machining operations by tilting or rotating the cutting tool, enabling access to additional surfaces of the workpiece.
5-Axis Milling: Offers the highest level of machining versatility, as the cutting tool can move in multiple directions simultaneously. This enables the machining of highly intricate parts with complex geometries, reducing the need for multiple setups and increasing efficiency.
Complexity of Parts
3-Axis Milling: Suitable for parts with simple geometric features and flat surfaces.
4-Axis Milling: Enables machining of more complex parts with features that require CNC machining from multiple angles.
5-Axis Milling: Ideal for producing high-precision parts with intricate contours, undercuts, and features that would be challenging or impossible to machine using fewer axes. Allows for the creation of parts with smoother surfaces and tighter tolerances.
Setup and Programming
3-Axis Milling: Generally simpler setup and programming compared to multi-axis milling operations.
4-Axis Milling: Requires additional considerations for toolpath generation and workpiece orientation but is still manageable with standard CAM software.
5-Axis Milling: More complex setup and programming due to the increased degrees of freedom. Requires specialized computer-aided manufacturing (CAM) software and expertise to generate optimal toolpaths and ensure efficient machining.
Here’s a comparison of 5-axis Milling with 3-axis and 4-axis Milling in a table format:
Aspect 3-Axis
Milling 4-Axis
Milling 5-Axis Milling
Number of Axes 3 (X, Y, Z) 4 (X, Y, Z, Additional rotary axis) 5 (X, Y, Z, Two additional rotary axes)
Setup and Programming Generally simpler setup and programming compared to multi-axis milling operations Requires additional considerations for toolpath generation and workpiece orientation but manageable with standard CAM software More complex setup and programming due to increased degrees of freedom, requiring specialized CAM software and expertise.
Complexity of Parts Best suited for simple geometric features and flat surfaces Enables machining of more complex parts with features that require machining from multiple angles It is ideal for producing highly complex parts with intricate contours and undercuts.
Machining Capabilities: Suitable for simple parts with flat or prismatic geometries Enables machining from multiple angles, facilitating access to different sides of the workpiece Allows simultaneous movement in multiple directions, machining highly intricate parts with complex geometries.
Best Practices for Implementing 5-Axis Milling:
Manufacturers can effectively implement 5-axis milling technology, unlocking its full potential and achieving superior results in precision, efficiency, and part quality. Here are tips on how to implement 5-axis Milling:
Proper Machine Selection
Selecting the right 5-axis milling machine is critical for successful implementation. Consider factors such as machine rigidity, spindle power, tool capacity, and axis travel to ensure alignment with specific application requirements. It’s essential to choose a machine that can handle the complexity and size of the intended parts for production.
Operator Training and Skill Development
Invest in comprehensive training programs for operators to ensure they have a solid understanding of 5-axis milling principles and are proficient in operating the machine and CAD/CAM software. Continuous skill development is key to keeping operators updated with the latest techniques and advancements in the field.
Optimize Toolpath Generation
Utilize advanced CAD/CAM software with simulation capabilities to generate optimal toolpaths for 5-axis Milling. Take advantage of toolpath optimization features to minimize tool deflection, vibration, and machining time while maximizing surface finish and tool life.
Rigorous Quality Control Processes
Establish stringent quality control processes to ensure that parts meet required specifications and tolerances. Implement in-process inspection techniques such as probing and laser scanning to monitor part dimensions and detect deviations during machining.
Maintain Machine and Tooling
Adhere to regular maintenance schedules to keep the 5-axis milling machine in optimal condition and prevent unplanned downtime. Monitor tool wear and replace cutting tools as needed to maintain machining accuracy and surface finish.
Collaborate with Suppliers and Partners
Forge close partnerships with tooling suppliers and CAD/CAM software providers to stay informed about the latest advancements and best practices in 5-axis Milling. Collaborate with machining experts and industry peers to exchange knowledge and insights.
Continuous Improvement Culture
Foster a culture of continuous improvement within the organization by encouraging operators and engineers to propose and implement innovative solutions. Regularly review and analyze machining processes to identify areas for optimization and implement corrective actions as necessary.
The Future of 5-Axis Milling
The future of 5-axis Milling appears promising with technological advancements and heightened integration with automation and robotics. These enhancements will elevate the milling process by increasing speed, precision, and efficiency, thereby enabling manufacturers to produce complex parts effortlessly.
Advancement in Technology
In the coming years, 5-axis Milling will undergo significant technological advancements. Machines will enhance precision and speed due to progress in machine capabilities and tooling. This advancement will enable more efficient and accurate milling of complex parts. Moreover, there will be improved software for designing and controlling the milling process, simplifying the creation of optimal toolpaths and simulations for operators. Artificial intelligence will also contribute by predicting tool wear and optimizing milling processes, resulting in superior outcomes.
Integration with Automation and Robotics
Automation and robotics will have a profound impact on the future of 5-axis Milling. Machines will integrate with robotic systems capable of loading and unloading parts, changing tools, and conducting inspections. This automation will accelerate production and diminish the necessity for human involvement. Collaborative robots, or cobots, will collaborate with human operators to manage tasks like tool changes and part manipulation. Consequently, factories will operate smoothly with reduced manual labor, leading to heightened productivity and efficiency.
Conclusion
Five-axis milling has become essential across various industries, including medical technology, the aerospace industry, precision mechanics, mold-making, and automotive production. Some projects need the extra two axes for their advanced needs, while others benefit from less work and fewer mistakes. Adding a 5-axis machine might even let you make new things you couldn’t before.
No matter what you focus on, it’s worth thinking about using this handy and efficient technology. The success of 5-axis Milling isn’t solely dependent on technology; it also requires a proficient team with extensive expertise. Without a skilled workforce, achieving optimal results with this advanced manufacturing process is unattainable. At XTJ, we prioritize continuous training for our employees to ensure excellence in complex parts production. Contact us today to find out more about 5-axis Milling.