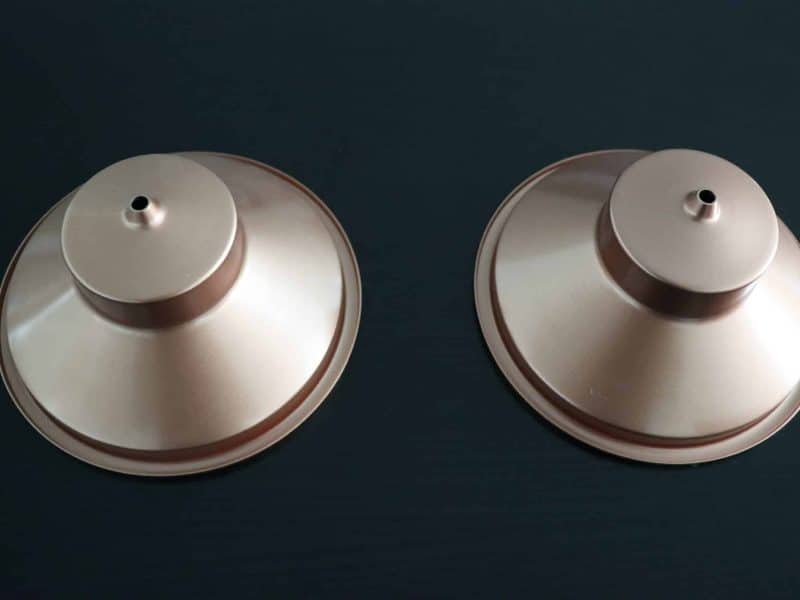
What is Casting Processes?
Casting Processes is but one method of metal shaping, as there are many other options, including welding, forging, stamping, extrusion and machining. Before settling on casting, you should first understand the benefits that the process provides over these other techniques. The casting process:
Ability to create complex geometries: Liquid metal facilitates construction of intricate designs, in either simple or complex geometries.
Fast production cycles: Once the casting tools are in order, very little maintenance and downtime is necessary. This makes casting an option for mass production applications.
Workability of hard metals: Casting is often one of the only viable manufacturing processes for hard metals that are not malleable enough for solid state shaping.
Reduced assembly: Oftentimes, casting can creatle items in a single, complete component, eliminating the need to assemble multiple pieces.
Minimal sizing restraints: Casting can create extremely small to extremely large parts, even up to 200 tons.
Versatile surface textures: Casting molds can be designed to deliver smooth, semi-smooth or rough surface textures.
Casting is a basic manufacturing procedure that entails molding molten material into the desired shape inside of a mold. There are different types of casting processes, including: sand casting, die casting, and investment casting. Each method offers various solutions for various industries while boasting its own advantages and disadvantages. For example, sand casting involves creating a mold out of sand, while die casting involves using metal molds for high-volume production. Investment casting is known for its intricate designs, which combine wax patterns with ceramic molds.
Type of casting process
Sand Casting
The versatile metal forming technique of sand casting uses non-reusable sand molds to produce intricate metal castings. It’s an essential method for creating metal parts in various sizes, ranging from ounces to tons. This technique is indispensable in many different industries because it excels at shaping alloys with high melting temperatures, such as: steel, nickel, and titanium. Inexpensive and recyclable materials are combined to make up molding sand with exceptional heat resistance. Silica is the preferred casting sand, though chemically bonded systems and green sand are also used. The effectiveness of the mold in maintaining its shape and producing high-quality castings depends on key characteristics like strength, permeability, and flowability. To learn more, see our guide on Sand Casting Manufacturing.
Die Casting (Metal Die Casting)
Die casting is a precision-focused manufacturing process that involves melting a metal with low melting point and injecting it into a long-life die-casting mold. These steel molds, which are created using cutting-edge techniques like CNC machining, guarantee high levels of accuracy, precision, and repeatability when creating metal components. The process has a long history that dates back to the 19th century. It has developed into two separate procedures: hot chamber and cold chamber die casting. Based on their different melting points, each process can handle a variety of materials, including: aluminum in cold chamber casting and alloys of zinc, tin, lead, and magnesium in hot chamber casting. Die casting finds extensive use in industries ranging from consumer and automotive products to aerospace components, making it an indispensable part of modern manufacturing.
Investment Casting
Investment casting, a meticulous method, crafts ceramic molds around wax patterns, in order to serve as encasements for molten metal. Multiple wax patterns can be melted onto a gate system, and then a layered casing is created by submerging the pattern(s) in slurry and sand. After the wax is removed, molten metals like stainless steel or aluminum are poured in to create intricately detailed copies. Investment casting efficiently creates complex parts that are difficult for other processes to produce; the advantages include: undercuts, fine detail, and smooth finishes. Investment casting has developed from its ancient roots to modern applications to become an essential technique used in a variety of industries, preserving fine craftsmanship and enabling effective large-scale manufacturing. To learn more, see our guide on What is Investment Casting.
Gravity Die Casting
The time-tested metal casting method known as gravity die casting uses gravity to introduce molten metal into a mold’s cavity. This approach, which has roots in antiquity, offers simplicity and economics. Manufacturers coat the cavity, melt the metal, pour it in, and then wait for the metal to solidify. The process uses automatic or manual machines. Positive mechanical characteristics, lower costs, and improved finishing are all advantages. The drawback of gravity die casting, however, is the length of time required to make intricate parts. Despite technological advancements, this seemingly crude method is still effective for smaller parts, finding use in a variety of applications including: kitchenware, lighting, and automobiles. Alternatives like aluminum die casting and sand casting are preferable for complex, high-volume production.
Continuous Casting
Continuous casting creates uniform, fine-grained, solid shapes with superior physical properties by quickly cooling molten metal inside a vertical or horizontal mold. This technique minimizes contaminants while maximizing yield because it uses gravity to ensure a steady flow. Although various configurations like squares and hexagons can be made, tubes and solids are the most typical shapes. When the metal has cooled after entering the mold and reached the desired length, it is continuously extracted. Continuous casting excels at producing high-density, pressure-resistant products for applications requiring precision and structural integrity. While continuous casting provides benefits like effective stock utilization and dimensional consistency, mold costs and suitability for particular alloys and quantities should be taken into account.
Shell Molding
A thin mold is made around a heated metal pattern as part of the precision casting process known as shell molding. Dry silica sand combined with a thermosetting resin forms a shell—that is about 6 mm thick—around the pattern. This shell is then dried, stripped, and joined to form a cavity for pouring molten metal. For the mass production of thin-walled castings, shell molding is the best option because it offers dimensional accuracy and a superior surface finish. Despite being more expensive than green-sand molding, it produces metallic patterns with high-quality results that guarantee intricate details and reliable results.
Lost-Foam Casting
In lost-foam casting, molten metal is poured into a foam mold (that evaporates during the pour) which is encased in sand. The mold is made of carved, machined, or injection-molded polystyrene foam. The waste gas can escape into the sand because the ceramic refractory coating is made permeable to a degree. The lost-foam casting process allows for complex shapes and thin walls at a lower cost and with less lead time and machining requirements than many other casting methods. Complex CAD designs and constrained part sizes, however, present difficulties. This process is used by a variety of industries, including: the arts, defense, and automotive, to produce a wide range of parts, including circuit boards, sculptures, and automobile components.
Pressure Die Casting
Modern metal processing methods like high-pressure die casting involve quickly and rapidly filling a mold with molten metal to create castings. It boasts strong mechanical properties, minimal machining, high production efficiency, and excellent surface finish. Key process parameters include: time, temperature, speed, and pressure. Filling capacity and specific pressure have an impact on compactness. Mold temperature has an impact on cooling speed and surface quality. The manufacturing of toys, appliance parts, and automotive housings are just a few examples that make use of pressure die casting.
Centrifugal Casting
The centrifugal casting method, also referred to as roto casting, is used to create thin-walled cylinders from materials like metal, glass, and concrete. It produces a fine-grained casting with rotational symmetry by rapidly rotating a permanent mold while pouring molten material. Instead of producing custom-shaped parts, the centrifugal casting method is often employed to produce standardized stock materials for further machining. It was created in 1852 by Alfred Krupp and is used to make things like pipes, flywheels, and cylinder liners.
Permanent Mold Casting
Permanent mold casting is a method of casting metal that produces accurate, high-quality castings using reusable molds made of materials like steel or iron. It is widely used in sectors like automotive and aerospace that demand complex shapes, large volumes, and superior mechanical properties. Cost-effectiveness, fine-grained structures, smooth finishes, and intricate designs are some of its advantages. Initial costs, a lack of material compatibility, and problems with heat transfer are obstacles. Innovations include CAD, hybrid processes, and 3D printing for making molds. Applications benefit from improved durability, accuracy, and customization in the automotive, aerospace, and medical industries. To learn more, see our guide on Permanent Mold Casting.
Vacuum Casting
Vacuum casting, also known as polyurethane casting or urethane casting, uses silicone molds to produce rubber and plastic components in a vacuum. This adaptable method creates bubble-free castings with smooth surfaces by mimicking injection molding. Rapid prototyping and low-volume production of complex parts benefit the most from its use. Numerous resin options are available for vacuum casting, which also has uses in the automotive, aerospace, and product design verification industries. Vacuum casting has advantages in terms of flexibility and cost-effectiveness, but it’s important to take mold wear and shrinkage rate into account. The ability to produce intricate features and additive manufacturing are examples of innovations.
Low-Pressure Casting
Low-pressure die casting (LPDC) is a metal casting process in which molten metal is poured into a die-cast mold at low pressure, typically 20 to 100 kPa. This method continuously fills the die cavity to account for volume shrinkage during solidification, maintaining high accuracy. The castings are pure due to LPDC producing little slag and less oxidation. LPDC is particularly adept at creating intricate geometries with sharp contours and smooth surfaces. It has limitations in the production of thin-walled parts and slower cycle times, despite its benefits in accuracy and formability. Automotive parts like cylinder heads, blocks, and wheels, as well as everyday kitchen appliances like pressure cookers, are just a few examples of the many applications in which LPDC can be used. To learn more, see our guide on Low-Pressure Casting.
Squeeze Die Casting
Squeeze die casting, a combination of casting and forging processes, uses high pressure to solidify molten metals between hydraulic press plates. It produces nearly net-shaped casting that is almost pore-free and highly dense. The two primary types, direct and indirect, each have unique advantages. Indirect casting is similar to high-pressure die casting, whereas direct casting involves pouring metal into the die and pressing it under pressure. The process results in improved mechanical properties, shorter production cycles, and better metallic properties. Material selection varies, with aluminum, magnesium, and copper as common choices. Squeeze casting finds applications in automotive parts, aircraft components, and more.
How to casting Proces Step by Step?
casting Process is one of the oldest and most widely-used methods of metal casting, dating back to around, and even before, 10,000 BC.
The process employs sand for the main mold material, as this material can be shaped and compacted to form a variety of complex and large cavities for molten metal that will eventually be turned into metal castings for a host of different applications across numerous industries.
Sand casting consists of eight main steps, each of which will be covered in the following sections of this guide.
With an understanding of how this process works in a step-by-step manner, you’ll have the information you need to better decide whether or not this ancient casting method is the right fit for your next custom metal parts project.
Step 1: Pattern Creation
The sand casting process begins with the creation of a pattern, which is a replica of the final product that is to be cast.
Since the pattern is used to shape the mold cavity, it must have the same dimensions and shape as the final product, yet will usually be slightly larger to account for the shrinkage of the metal as it cools.
Patterns can be made from various materials, depending on the complexity and size of the product.
The most common types of materials used for creating patterns include wood, plastic, and metal, and the choice of which material to use for the pattern will depend on the requirements of the project.
Whichever the choice of material, the pattern will always include certain features that help with the molding process.
For example:
The pattern must have a taper or draft angle that is slightly sloped to make it easier to remove the pattern from the mold.
The pattern must have some holes or pins to align the two halves of the mold.
The pattern must have some extra projections or extensions, which form channels for the molten metal to enter and air to escape from the mold.
The following steps are taken to create the pattern during sand casting:
1. The material and design are chosen for the pattern.
2. The sand and the molding box are prepared.
3. The pattern is placed in the drag and the sand is packed around it.
4. The drag is turned over and the pattern is removed.
Creating the pattern is not only the first step in sand casting but also one of the most important ones, as it establishes the shape of the final product, albeit with some slight modifications to adjust for shrinkage.
Step 2: Mold Preparation
After the pattern has been created, the mold is prepared, which will further give the molten metal its desired shape.
The mold is typically made of two halves —the cope and drag—with the cope being the upper half, and the drag the lower half.
The cope and drag help form the cavity where the molten metal will be poured to create the desired shape of the casting.
To create the mold, sand is mixed with a binder, made of either clay or resin, to make it more cohesive and strong.
The sand that is used for creating the mold must be fine-grained and uniform in size to create a mold cavity with greater details and higher temperature resilience.
Aside from sand, sand-casting molds will also include the following elements:
Cavity (pattern & compacted sand)
Gating System
Cores
Risers
Flask (cope & drag)
Without the above elements, the proper shape and temperature settings cannot be reached.
As for the specific steps required to prepare and make the mold, the following process is used:
1. The sand is packed around the pattern in a wooden or metal box called a flask. The flask has holes or vents to allow air and gasses to escape.
2. The mold cavity is inspected for any defects or irregularities.
3. The two halves of the mold are aligned and joined together.
A sprue is usually made in the scope to allow the molten metal to enter the mold.
Without the mold, the pattern would not hold and the desired shape could not be accomplished, which is why the above-mentioned process of preparing the mold must be strictly adhered to secure the proper temperature-resistance and formation of the end product.
Step 3: Core Making
The third step of the sand casting process (i.e. core making) involves creating the internal features of the final product that cannot be formed by the mold cavity alone.
Cores are inserts made of sand or other materials that are placed into the mold to create voids (cavities) within the final casting.
Cores are made by using a core box, and the uses of core boxes are many:
uses of core boxes
The following steps are involved in creating the core box:
1. The core box is filled with core sand (sand with binder),
2. The core sand is compacted and shaped by the core box and then removed and baked to harden it.
3. The hardened core is then placed into the mold cavity before pouring the molten metal.
Core making is a very important step in the sand-casting process because it allows for more complex and intricate designs to be produced.
However, this step will add more cost and time to the process, and therefore should only be used when the overall casting quality and efficiency need to be increased.
Step 4: Assembling the Mold
During this step of the sand casting process, the mold and cores are put together to form the final shape of the casting.
This is a crucial step, as any misalignment or defect in the mold assembly can affect the quality and accuracy of the final product.
To assemble the mold, the following steps are taken:
1. The cope and drag are aligned and checked carefully for any gaps to avoid leakage and distortion of the molten metal.
2. Channels (runners and gates) are created and added for the molten metal to flow into and fill the mold cavity.
3. The cores are placed inside the mold cavity firmly in place, as any movement or displacement can cause defects in the casting.
Following the above three steps is necessary to ensure that the mold has the correct shape and dimensions for producing high-quality casting.
Failing to assemble the mold properly can lead to a variety of casting defects which can compromise not only the shape, size, and dimensions of the cast part but its quality and functionality, too.
Step 5: Metal Melting and Pouring
Melting and pouring the metal requires attention and preparation, as not doing so can lead to many issues negatively affecting the quality of the final product, efficiency of the process, and safety of employees.
As far as cast quality is concerned, any error during this step of the sand-casting process can result in the following issues:
Errors during Metal Melting and Pouring
To avoid the above problems, the following tips should be considered before the melting and pouring begins:
The correct temperature for melting the metal must be maintained as different metals and alloys require different temperatures to melt.
Workers must use heat shields and other safety equipment to protect themselves from the high temperatures and potential splashes of molten metal.
Gasses emitted from the sand mold need to be properly managed to avoid defects in the casting.
Additives such as fluxes can be added during pouring to prevent oxide formation.
Eco-friendly casting techniques can be used to help minimize waste, maximize efficiency, and lessen environmental impact.
This step of the sand casting process consists of several procedures that can be split up into two major phases: melting and pouring.
Melting
1. The appropriate metal for the casting is selected. A metal chart or a professional metal manufacturer can be consulted to aid in this decision.
2. A furnace that can heat the metal to its melting point is selected. The furnace can be gas-fired, electric, or induction-based, depending on preference and budget.
3. The metal is placed inside a crucible and the furnace is turned on. The temperature and the time of the heating process must be monitored carefully to ensure that the metal reaches its melting point and becomes completely liquid.
Once the metal is fully melted, the pouring phase begins.
Pouring
1. The molten metal is poured slowly and steadily into the mold cavity through a gating system, filling it up completely.
2. The metal is allowed to solidify in the mold for a certain period.
As can be seen from the above process, melting and pouring the mold requires many steps that need to be followed to the letter to ensure the quality of the cast, efficiency of the process, and safety of the workers involved.
Failure to do so can potentially jeopardize not only the final product but also the health of all of those involved in casting it.
Step 6: Metal Cooling
In the sixth step, the molten metal that was poured into the mold cavity begins to cool and solidify.
During this stage, the cooling rate is the most important factor, as it directly affects the microstructure and properties of the final casting.
Defects such as shrinkage, porosity, cracks, and distortion may occur if the metal cools too fast or too slow.
Several conditions influence the rate of cooling, including:
The type and composition of the metal or alloy.
The size and shape of the casting.
The design of the gating system.
The type and quality of the sand mold.
It is important to note here that, if a harder cast is desired, then the rate of cooling must be sped up.
In this instance, processes such as quenching can be added to accomplish this task.
Once the metal has been cooled, it is allowed to solidify into a solid casting that is identical to the shape of the mold cavity.
After solidifying, the casting is then removed from the mold by breaking or shaking off the sand.
The unique feature of sand casting is that the sand can be reused for making new molds after some cleaning and reconditioning.
Once solidification has been achieved, the second to last step of the process begins.
Step 7: Shakeout and Cleaning
Shakeout and cleaning involve removing the casting from the mold and getting rid of any unwanted material that may have stuck to it during the previous steps.
Shakeout helps eliminate galvanizing embrittlement and cleaning helps improve the quality of the surface finish of the casting.
Aside from reducing embrittlement and a poor surface finish, the shakeout and cleaning process can also assist in the reclamation of sand, as well as proper material handling which can greatly reduce safety risks and material costs.
To ensure a proper shakeout and cleaning process, the following tips are suggested:
The mold should be broken open only after the metal has completely solidified to prevent any deformation or damage to the casting.
A hammer can be used to break open the mold gently and carefully – if too much force is used on the casting directly, it may cause cracks and defects to occur.
Upon removal, the cast should be inspected for any defects (e.g. porosity, shrinkage, and misalignment).
Any excess material, such as sand, cores, or gates, should always be cleaned from the casting.
To clean excess material manually, a wire brush, a chisel, or a grinder can be used, whereas a shot blaster, a tumbler, or a sandblaster can be used to clean them automatically.
The surface finish of the casting should be checked with a profilometer to measure the surface roughness.
If the surface finish is not satisfactory, additional processes such as polishing, grinding, or coating may be needed to improve it.
The shakeout and cleaning process may vary depending on the type of metal, mold, and casting requirements.
However, it will generally involve the following steps:
1. A punchout ram is used to push the casting out of the flask while breaking up the sand mold.
2. The sand is separated from the casting by using a vibrating deck or a rotary drum.
3. High-pressure air or water is used to propel abrasive particles (e.g. sand, steel shot, and glass beads) at the casting.
4. Saws, shears, chisels, and torches are used to remove sprue, risers, gates, and other unwanted metal parts from the castings.
The process may involve as little or as many tools as needed to fully clean the casting and reveal the state of the surface and the overall quality of the final product.
However, if the surface finish is deemed insufficient, then the eighth and final step of the sand casting process will be needed.
Step 8: Finishing
The last step of the sand casting process consists of finishing the metal part.
This final step is needed if there is still “extra” material clinging to the casting even after cleaning it or if there are any rough patches on the surface of the cast.
Finishing can be done by various methods depending on the type of metal, the shape and size of the part, and the desired quality and appearance of the final cast.
The most common finishing techniques that are used in sand casting are:
Machining: The process of cutting, drilling, milling, or turning the metal part using a machine tool.
Grinding: The process of using an abrasive wheel or belt to smooth or polish the surface of the metal part.
Coating: The process of applying a layer of another material on the surface of the metal part to make it more appealing and improve metal properties such as corrosion resistance, wear resistance, and electrical conductivity,
Some examples of coating materials are paint, zinc, chrome, and nickel.
While the above finishing methods are the most common ones used in sand casting, other finishing techniques may be used to further enhance the surface of castings.
Some of these include:
Heat Treatment
Sand Blasting
Shot Peening
Electroplating
If the surface finish does still not meet the requirements after the finishing process has been completed, then it gets repeated until it does.