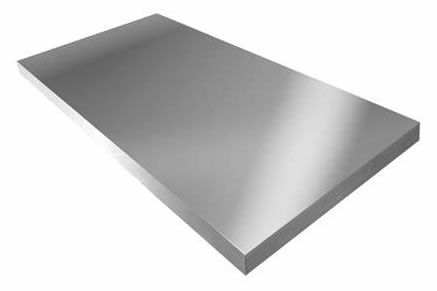
Table of Contents
What is 5052 Aluminum?
5052 aluminum comes in many types, known as alloys, and each provides unique benefits depending upon the alloy chosen. An alloy is an enhanced engineering material, made by adding unique elements into a base metal. In this article, the base metal in question is aluminum, and these unique elements can be silicon, copper, zinc, and/or many other metallic elements. These “alloying” elements may increase the strength, conductivity, resilience, or chemical properties of the base metal, and can make it more versatile as an engineering material. Aluminum is easily alloyed, so there are numerous series of aluminum alloys that have been organized by The Aluminum Association (AA Inc.) based on their alloying elements, and each given a four-digit name. 5052 aluminum alloy will be the main focus of this article, which comes from the 5xxx series of aluminum alloys, or those which use magnesium as their primary alloying element (for a better understanding of the nomenclature of aluminum alloys, please visit our article all about 6061 aluminum alloy). The physical, mechanical, and chemical properties of 5052 aluminum will be highlighted in this article to show that it is an invaluable resource to some vital applications.
Physical Properties of 5052 Aluminum
As explained previously, aluminum alloys have specific percentages of alloying elements that improve material properties; these percentages are important, because they differentiate one alloy from another, especially within the same series. Type 5052 aluminum contains 97.25% Al, 2.5%Mg, and 0.25%Cr, and its density is 2.68 g/cm3 (0.0968 lb/in3). Generally, 5052 aluminum alloy is stronger than other popular alloys such as 3003 aluminum and also has improved corrosion resistance due to the absence of copper in its composition.
The properties of 5052 aluminum alloy differ based on how it is cold worked, or made stronger using the work-hardening process. When worked, or permanently altered in shape (think bending, forming, rolling, etc.), metals such as aluminum will increase in strength but decrease in malleability. This is a consequence of the metal’s molecular structure, but for the brevity of this explanation, just know that there are mechanical methods to making aluminum alloys stronger. There are several different procedures to work-harden 5052 aluminum alloy, but this article uses the strength values from H32 hardened 5052 aluminum alloy (5052-H32). Note that this alloy cannot be strengthened using the heat-treatment process, which other aluminum alloys such as 7075 aluminum or 6061 aluminum benefit from (more information on heat-treatment can be found in these respective articles).
Mechanical Properties
There are some important metrics to know when understanding the mechanical properties of an engineering material, and they are all summarized in Table 1 below.
The first two important values are the modulus of elasticity and the shear modulus, which represent a material’s response to axial (pulling/pushing) and shearing (twisting/cutting) forces, respectively. These measures are found empirically using stress tests, and 5052 aluminum’s modulus of elasticity and shear modulus are found to be 70.3 GPa (10,200 ksi) and 25.9 GPa (3,760 ksi), respectively.
The yield strength and ultimate strength are also central values to know when specifying a material. They represent the maximum amount of stress that causes elastic (non-permanent) and plastic (permanent) deformation. For a more in-depth understanding of these values, visit our article all about 7075 aluminum alloy. The yield strength is usually the most concerning value in static applications, where the material must never permanently deform (such as in structural applications). However, the ultimate strength may be necessary in specific instances, so it may not hurt to know it. 5052 aluminum alloy has a yield strength of 193 MPa (28,000 psi) and an ultimate tensile strength of 228 MPa (33,000 psi), which means it is moderately strong when compared to other some popular alloys.
Shear strength is the strength of a material when being “sheared” by opposing forces along a plane. 5052 aluminum alloy is often exposed to this stress, as it is commonly stamped from sheet metal plate. Essentially, the force of the stamp opposes the force of the plate on the work surface, shearing (or cutting), the metal through the perpendicular plane (or the thinnest dimension of the sheet metal). For a more intuitive understanding of these values, feel free to visit our article all about 6061 aluminum alloy. 5052 aluminum alloy’ shear strength is 138 MPa (20000 psi), which is again moderately stronger than some other common alloys.
Summary of mechanical properties for 5052 aluminum alloy.
Mechanical Properties | Metric | English |
Ultimate Tensile Strength | 228 MPa | 33000 psi |
Tensile Yield Strength | 193 MPa | 28000 psi |
Shear Strength | 138 MPa | 20000 psi |
Modulus of Elasticity | 70.3 GPa | 10200 ksi |
Shear Modulus | 25.9 GPa | 3760 ksi |
Corrosion Resistance 5052 Aluminum
5052 aluminum alloy is especially useful because of its increased resistance to caustic environments. All aluminum alloys form an oxide layer in the presence of air/water, which protects the chemically-active aluminum from further reacting with the outside environment. The amount of corrosion resistance is dependent upon temperature, airborne chemicals, and the proximal working environment; however, under ambient circumstances, 5052 aluminum holds up exceptionally well. Type 5052 aluminum does not contain any copper, which means it does not readily corrode in a saltwater environment that can attack and weaken copper metal composites. 5052 aluminum alloy is, therefore, the preferred alloy for marine and chemical applications, where other aluminum would weaken with time. 5052 aluminum in the presence of alkaline soil may cause corrosive effects such as pitting, but this is difficult to generalize due to high variation in soil compositions. Due to its high magnesium content, 5052 is particularly good at resisting corrosion from concentrated nitric acid, ammonia and ammonium hydroxide. Any other caustic effects can be mitigated/removed by using a protective layer coating, making 5052 aluminum alloy highly attractive for applications which need an inert-yet-tough material.
Applications of 5052 Aluminum
5052 aluminum is stronger than other popular alloys and has increased corrosion resistance. These characteristics allow 5052 aluminum to excel in the marine industry as well as in electronics and chemical applications. The uses of 5052 aluminum are vast, but some notable applications include:
Pressure vessels
Marine equipment
Electronic enclosures
Electronic chassis
Hydraulic tubes
Medical equipment
Hardware signs
XTJ is a leading OEM Manufacturer that is dedicated to providing one-stop manufacturing solutions  from prototype to production. We are proud to be an ISO 9001 certified system quality management company and we are determined to create value in every customer relationship. We do that through collaboration, innovation, process improvements, and exceptional workmanship.