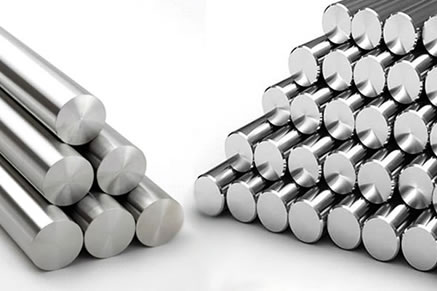
Table of Contents
What is Aluminum ?
Aluminum is the most abundant metal on Earth, giving material scientists many chances to experiment with it in the alloying process.
Alloys are metals with enhanced material properties (strength, resistance, workability, etc.), made by adding metallic elements into a base metal. Aluminum alloys come in many different forms based on their alloying components, and the Aluminum Association Inc. has organized these alloys into series based on these alloying elements. These series are given as four-digit names, and this article focuses on the 3xxx and 6xxx series.
The two alloys in question – 6061 and 3003 aluminum – are among the most popular aluminum choices, and at first glance, seem interchangeable. This article hopes to differentiate these two alloys using a comparison of their material properties, with a focus on their advantages and disadvantages. Through this discussion, this article will define the applications best suited for both of these alloys to help designers make more informed material choices for their projects.
6061 Aluminum alloy
6061 aluminum is famous for its high strength, good weldability and machinability, and good resistance to corrosion. It is especially useful in structural materials, as the strength of 6061 aluminum helps keep tall buildings from falling over. Like the other 6xxx alloys, 6061 aluminum contains magnesium and silicon as its main alloying elements, and they are responsible for its favorable strength characteristics. The breakdown of the alloying elements in 6061 aluminum is as follows: 0.6% Si, 1.0%Mg, 0.2%Cr, 0.28% Cu, and 97.9% Al, and its density is the about the same as pure aluminum (2.7 g/cm3, 0.0975 lb/in3). 6061 aluminum gets even larger strength gains with the heat treatment process and is commonly found in T6 and T4 tempers. Its benefits have allowed 6061 aluminum to work many situations, making it a great general-use alloy. It can be found in most machine shops and is a top choice for welded assemblies, building frames, or any structure that needs a rock-solid skeleton. For more information on this metal, feel free to check out our article all about 6061 aluminum alloy.
3003 Aluminum alloy
3003 aluminum alloy is one of the most widely distributed types of aluminum on the market today and for good reason. It takes a good finish, has excellent formability, welds well, has moderate strength, and resists corrosion. These attributes allow this metal to succeed in a variety of applications and is why it is considered the most popular general-use aluminum alloy. 3003 aluminum is of the 3xxx series, meaning its main alloying element is manganese, and its chemical composition is 0.12% Cu, 1.2% Mn, and 98.6% Al (note that these numbers change based on a number of factors, and only provide a general breakdown). The density of 3003 aluminum is 2.73 g/cm3 (0.0986 lb/in3), which is around the same as pure aluminum, and it does not respond to the heat treatment process. Instead, this alloy can be strain-hardened to increase its strength, and usually comes in 3003-H18 and 3003-H22 tempers. While not especially strong, 3003 aluminum has many applications in the food/chemical markets and is useful as a highly-malleable yet resistant material. For more information about this alloy, check out our article all about 3003 aluminum alloy.
Comparing 6061 & 3003 Aluminum alloys
Choosing between these two aluminum alloys is often difficult, as they are both great choices for most projects and have similar qualities. This article will compare some important mechanical values to help distinguish these two metals, and these comparisons will help determine which is the best fit for any given application. The values found in Table 1 were taken from 6061-T6 and 3003-H18 treated aluminum, but know that these numbers fluctuate based on which temper is chosen. These values are summarized in the below table, and a discussion of their comparisons will follow shortly thereafter.
Comparison of material properties between 6061 & 3003 aluminum alloys
Material properties |
Type 6061 Aluminum alloy |
Type 3003 Aluminum alloy |
||
Units |
Metric |
English |
Metric |
English |
Yield Strength |
276 MPa |
40000 psi |
185 MPa |
26800 psi |
Bearing Yield Strength |
386 MPa |
56000 psi |
262 MPa |
38000 psi |
Shear Strength |
207 MPa |
30000 psi |
110 MPa |
16000 psi |
Hardness (Brinell) |
95 |
55 |
||
Machinability |
Good |
Fair |
The primary reason to choose 6061 aluminum over 3003 aluminum is its superior strength. This is shown by comparing their yield strengths, which is the minimum amount of stress that will cause these materials to permanently deform. The yield strength is a useful measure for structural parts, as any permanent deformation will cause instability (and often failure) in a building. The increased strength of 6061 aluminum is a consequence of its alloying elements (magnesium/silicon), as well as its ability to be heat-treated. If strength is a major concern, look no further than 6061 aluminum; it is a strong, more resistant alternative to mild steels and is decidedly stronger than 3003 aluminum.
Similarly, 6061 aluminum is stronger when joined via bolts and screws, and this shown through its increased bearing yield strength (386 MPa VS. 262 MPa). The bearing yield stress describes the minimum stress that will cause a joint to deform, such as when two plates are connected by a screw through a hole in both plates. These joints can stretch or crack if excessive force is imparted on the metal pieces, and the bearing strength is a useful measurement to determine how a material will react when joined. 6061 aluminum’s bearing yield strength is much higher than 3003 aluminum’s, which not only makes intuitive sense but also explains why 6061 aluminum is commonly used in scaffolding and building skeletons. If many parts will be riveted or held together by hole-connections, 3003 aluminum can still hold up, but 6061 aluminum will hold up longer.
Strength is not always desired, and the shear strengths of these materials are great examples of this concept. Shear strength is a measure of a material’s resistance to shearing stresses, such as cutting, stamping, or any arrangement where two opposing forces meet at a cross-section. An easy way to visualize this is scissors cutting paper, where the two opposing scissor blades shear, or “cut” the paper through its thinnest dimension. The lower shear strength of 3003 aluminum is actually a benefit, as it is easier to cut from sheet metal than 6061 aluminum due to its lower shear strength (207 MPa VS. 110 MPa). Combined with its great formability, these characteristics make 3003 aluminum particularly versatile in forming applications and is often a reason for choosing it over other alloys.
Hardness is a measure of how a material’s surface responds to local indentation such as scratching, polishing, and penetration, and it describes how outside forces will affect the material. Engineers have determined different hardness scales that describe how materials respond to indenting forces using indentation machines. The Brinell hardness scale is a commonly used measurement system, where a material like glass has a Brinell hardness of ~1550 while a soft metal like copper is around 10. These alloys are somewhat hard, with 6061 aluminum being the harder of the two (95 vs. 55), which increases its machinability but decreases its surface finish. While more easily indented, 3003 aluminum can come to a chrome finish, which is aesthetically pleasing and easy to clean. 3003 aluminum is often seen in food trucks as a result, as the reflective surfaces are quick to clean and do not collect dirt. 6061 aluminum should be chosen over 3003 if scratch resistance is of any concern, but it is outshined (literally) by 3003 when it comes to finishing/polishing.
6061 aluminum can be found in almost every machine shop, as it is one of the best machining alloys available. Machinability is a measure of how well a metal can be tooled from stock metal, and this article uses a qualitative evaluation (excellent/good/fair/poor) to give the reader an idea of what alloys are commonly machined. There are scales that quantify machinability, but they usually just concern machinists looking for the right tool for the job and are not useful to the average designer. 6061 aluminum is a premier choice for machining because it machines and takes finishes well, while 3003 aluminum is usually reserved for sheet metal forming. 3003 aluminum can also be machined, but 6061 is an overall better choice because of its other complementary attributes.
XTJ is a leading OEM Manufacturer that is dedicated to providing one-stop manufacturing solutions  from prototype to production. We are proud to be an ISO 9001 certified system quality management company and we are determined to create value in every customer relationship. We do that through collaboration, innovation, process improvements, and exceptional workmanship.